In today’s rapidly advancing technological world, industrial automation robotics has emerged as a game changer for industries worldwide. From automotive assembly lines to food packaging units, robots are transforming the way production is carried out. In this article, we will explore what industrial automation robotics is, its history, benefits, challenges, applications, and the future it holds for global industries.
1. What is Industrial Automation Robotics?
Industrial automation robotics refers to the use of robotic systems and automated machinery to perform tasks traditionally handled by human workers in industrial settings. These robots are designed to carry out repetitive, precise, and sometimes dangerous tasks with high speed, accuracy, and reliability. They are programmed to operate independently or alongside human workers, enhancing overall productivity and safety in manufacturing units.
2. A Brief History of Industrial Robotics
The journey of industrial robotics began in the 1950s when George Devol invented the first programmable robot called Unimate. By the 1960s, General Motors adopted Unimate for their assembly lines, marking the beginning of robotic automation in manufacturing. Over the decades, with advancements in microprocessors, AI, and sensor technologies, industrial robots have evolved into highly sophisticated machines capable of learning, adapting, and working collaboratively with humans.
3. Types of Industrial Automation Robots
There are various types of industrial robots, each designed for specific tasks:
a) Articulated Robots
These are the most common robots with rotary joints, widely used for welding, painting, and assembly.
b) SCARA Robots
Selective Compliance Assembly Robot Arm (SCARA) robots are ideal for pick-and-place tasks due to their flexibility and speed.
c) Cartesian Robots
Also known as gantry robots, they operate on three linear axes (X, Y, Z) and are used in CNC machinery and 3D printing.
d) Delta Robots
Lightweight robots used for high-speed picking and packaging applications.
e) Collaborative Robots (Cobots)
Cobots are designed to work safely alongside humans, assisting in assembly, packaging, and quality inspection tasks.
4. Key Benefits of Industrial Automation Robotics
Industrial automation robotics offers several benefits to industries across sectors:
- Increased Productivity: Robots can work 24/7 without fatigue, resulting in higher production rates.
- Enhanced Precision: They reduce human error, ensuring consistent product quality.
- Improved Safety: Robots handle dangerous tasks, minimising workplace injuries.
- Cost Efficiency: Though the initial investment is high, automation reduces long-term operational costs.
- Better Resource Utilisation: Robots optimise material usage and reduce wastage.
5. Applications of Industrial Automation Robotics
Industrial robots are used in various manufacturing processes, including:
a) Welding
Robotic welding ensures consistent weld quality and safety, especially in the automotive industry.
b) Assembly
Robots assemble complex components swiftly and accurately, improving product standards.
c) Material Handling
From packaging to palletising, robots manage heavy materials efficiently.
d) Painting
Robots provide uniform painting with minimal wastage, crucial in automobile and furniture manufacturing.
e) Quality Inspection
Robotic vision systems detect defects that are often missed by human eyes, ensuring high-quality output.
6. Impact on Workforce and Job Opportunities
A common misconception is that robotics eliminates jobs. In reality, industrial automation robotics creates new opportunities for skilled professionals. Industries now require robotics engineers, programmers, maintenance technicians, AI experts, and system integrators to design, operate, and manage robotic systems. Upskilling and reskilling programs are essential to prepare the workforce for this technological shift.
7. Challenges in Implementing Industrial Automation Robotics
Despite its benefits, industries face challenges while adopting robotics:
- High Initial Costs: Setting up robotics systems requires substantial investment.
- Skill Gap: Lack of trained professionals to operate and maintain robots.
- Integration Complexity: Merging new robotic systems with existing production processes.
- Maintenance Requirements: Regular servicing is crucial for uninterrupted operations.
- Cybersecurity Risks: As robots are connected to networks, they are vulnerable to cyber threats.
8. Future Trends in Industrial Automation Robotics
The future of industrial robotics is promising with emerging trends such as:
a) AI and Machine Learning Integration
Robots will become smarter with AI, enabling them to make real-time decisions and adapt to changing environments.
b) IoT Connectivity
Internet of Things (IoT) will connect robots with production systems for seamless data exchange and remote monitoring.
c) Human-Robot Collaboration
Cobots will continue to evolve, making collaboration safer and more efficient in complex tasks.
d) 5G Technology
With ultra-fast 5G networks, robots will communicate faster, enhancing automation in real-time applications.
e) Sustainable Robotics
Future robots will focus on energy efficiency and environmentally friendly operations, contributing to green manufacturing goals.
9. Top Companies Leading Industrial Automation Robotics
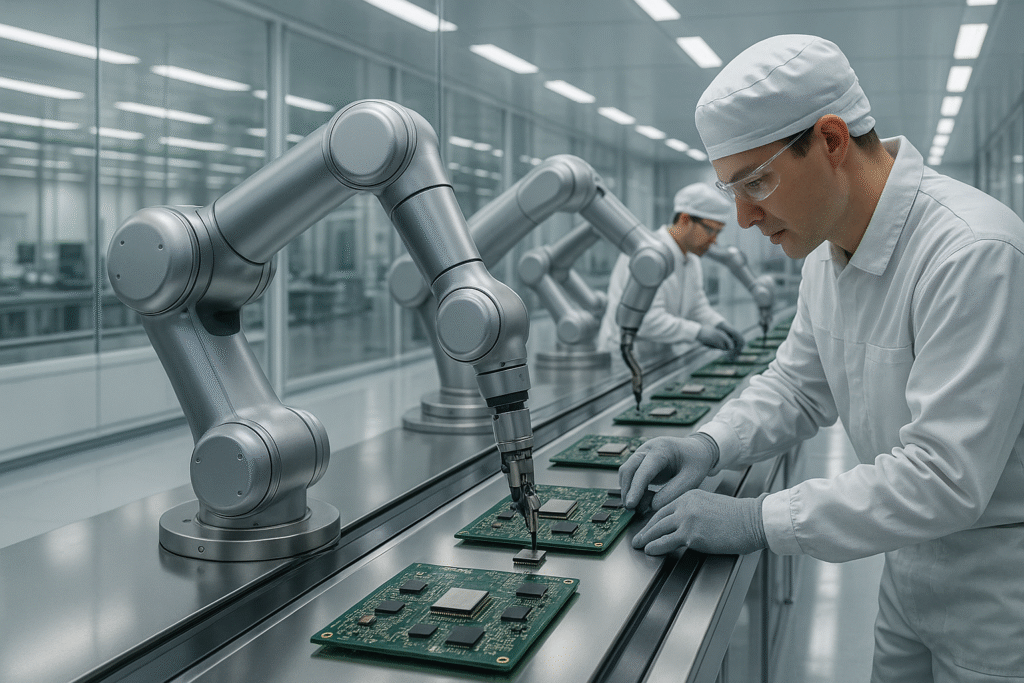
Some of the leading global companies in the robotics industry are:
- ABB Robotics: Known for flexible robot arms and automation solutions.
- Fanuc: Offers a wide range of industrial robots with AI capabilities.
- KUKA Robotics: Specialises in automotive and heavy industry robotics.
- Yaskawa Motoman: Leaders in welding, assembly, and packaging robots.
- Universal Robots: Pioneers in collaborative robotics for SMEs.
10. How Small Businesses Can Adopt Industrial Automation Robotics
Previously, robotics was limited to large industries, but now small and medium enterprises (SMEs) can integrate automation to remain competitive. Affordable cobots and modular robotics systems are making automation accessible. Leasing options, government subsidies, and robotics-as-a-service models further ease adoption costs, empowering small businesses to automate packaging, inspection, and assembly tasks effectively.
Conclusion
In conclusion, industrial automation robotics is revolutionising manufacturing by increasing productivity, ensuring safety, and enhancing product quality. While it presents challenges such as high costs and skill gaps, its benefits far outweigh the drawbacks. As technology continues to evolve with AI, IoT, and advanced sensors, robotics will play an even more crucial role in shaping the future of industries worldwide. For businesses aiming to stay ahead in this competitive era, investing in industrial automation robotics is no longer an option but a necessity for growth, sustainability, and global excellence.